Decontamination techniques
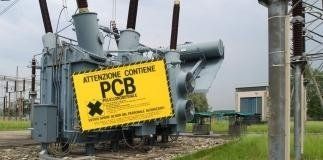
To resolve the problem of PCB in transformer oils (or other electrical equipment), it is necessary to fall below 50 mg/kg , better still below 25 mg/kg , in order to be able to transfer the oil free of charge to the Consortium of Used Oils (COOU).
For identification and selection of techniques of decontamination of PCBs, the Guidelines of the Ministry of Environment (Min. Decree 21/01/2007) is without doubt the reference document. This document identifies two types of alternative solutions:
- Replacement of the insulating liquid (Refilling) with new insulating liquid, and disposal of used insulating liquid as PCB waste. (COMBUSTION TECHNOLOGY).
- Dehalogenation (decontamination) of PCBs in insulating liquid in service, which makes it possible to keep contaminated oil in use after detoxification (elimination) of PCB treatment. (NON COMBUSTION TECHNOLOGY).
The main chemical processes currently available are:
- Processes of dehalogenation with sodium, lithium and derivatives, characterised by:
- dangerous liquid reagents based on metallic sodium, sodium hydride, lithium hydride
- a batch process that makes the whole activity all the more critical
- high average operating temperatures (150-300 °C), which increase the risk of explosions especially in the presence of water and air
- Processes of dehalogenation with polyethylene glycol and potassium hydroxide (KPEG in batch). This technique:
- uses a liquid reagent formed by polyethylene glycol (PEG) and a hydroxide of an alkaline metal (typically KOH), and thus presents a difficult separation of the liquid reagent and the reaction products from the insulating oil
- operates at temperatures of 130-150 °C
- has a limited efficiency on certain types of contaminants (Aroclor 1242)
- Process of continuous closed loop dehalogenation. This technology:
- uses a patented solid reactant, also effective on particularly stable aromatic halides
- operates at temperatures of 80-100 °C
- does not produce waste
- can be performed at the site of installation of the equipment to be decontaminated by closed oil circulation, without even partial emptying of the equipment.
The only technology that operates according to these characteristics is Sea Marconi's CDP Process®
In addition to listing and describing the different methods of decontamination of PCBs in detail, the Guidelines of the Ministry of Environment (Min. Decree 21/01/2007) also identify the strengths and weaknesses of the various techniques in relation to the criteria that each owner should consider, for example:
_Environmental aspects
Preference should be given to decontamination techniques that permit recovery of oil and machine compared with replacement and disposal of the insulating liquid (retrofilling). Additionally, preference should be given to techniques that operate on site without emptying the transformer because these reflect the principles of proximity, self-sufficiency and functional recovery enshrined in European Community directives. Finally, processes carried out in continuous closed loop, without emptying the devices, are inherently more secure against risks of spillage of liquids containing PCBs into the environment.
_Consumption of resources and environmental life cycle assessment
_Atmospheric emissions and noise
_Generation of waste
In this context, the differences between oil change and dehalogenation techniques are substantial.
Changing of the oil load involves the generation of hazardous waste (liquids containing PCBs and solvents) in a quantity equal to or exceeding the quantity of PCBs contained in equipment, as a result of repeated phases of emptying and washing of the equipment.
---
Techniques of dehalogenation with hydrides of alkali metals or polyethylene glycol and potassium hydroxide (which are NOT used by Sea Marconi) give rise to liquid and solid waste resulting from the phases of reaction, filtration and absorption in an amount less than the amount of decontaminated insulating liquid (10-15%) typically in relation to the initial PCB concentration and from the thresholds to be reached. However, the phases of transportation and disposal of waste containing sodium, lithium and derivatives are critical because of their intrinsic characteristic of being hazardous.
---
The technique of dehalogenation (which is that used by Sea Marconi) does not originate hazardous waste. The reagents and other materials used in the treatment may be used several times in similar decontamination processes until the end of their reagent properties.
_Analysis of risks for workers' safety and public health
_Risks of explosion and fire in equipment
_Risks of leaks and spillages into the environment
From this point of view, closed-loop decontamination techniques without even partial emptying of equipment are obviously to be preferred.
---
Oil change (refilling) is certainly the most penalised technique because of the handling and pouring of huge volumes of insulating liquids.
_Analysis of operating context and logistical constraints
_Certification
_Case history operational experience of operator
The Guidelines of the Ministry of Environment (Min. Decree 21/01/2007) conclude by indicating that the best available techniques (BATs) are:
- those that use continuous closed-loop dehalogenation, that is, Sea Marconi's CDP Process® for transformers or equipment both "in service" and "at end of life" that are PCB-contaminated
- oil replacement + CDP Process ® for transformer or equipment "in service" isolated in PCB
- decontamination + processes for the recovery of the solid materials constituting the machine for transformers or electrical equipment "at end of life" isolated in PCB