Causes and types of corrosiveness
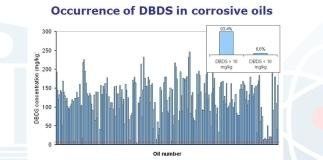
It is now known (IEC 60296 ed. 4 of 2012) that:
DBDS (added - without declaring so - by some manufacturers of oil to improve stability) tends to combine with the copper present in the transformer forming copper sulfide. The latter is deposited progressively right on the copper surfaces (in a manner similar to rust).
The process obviously occurs in different ways depending on the amount of DBDS and at different times depending on the temperature and the modes of operation of the transformer.
The copper sulfide then tends to detach from the copper and circulate dangerously in the oil, gradually being deposited within the highly porous insulating paperboards.
The natural consequence of this phenomenon is weakening of the insulation up to the electric arc and failure, with consequent direct damage (loss of the machine) and indirect damage (loss of production).
The corrosive sulfur compound, namely DBDS, has been found up to concentrations of 580 mg/kg both in new oils and in service. The analyses performed following failure have shown that 20 mg/kg of DBDS is sufficient to establish the first signs of corrosion on the copper.
In recent months, our R&D has also shown how there are enormous problems related to corrosiveness in non-naphthenic oils and, in any case, in products even before 1993, which is why Sea Marconi classifies corrosive oils into 4 different typologies:
- C1 - Corrosion with DBDS
- C2 - Corrosion without DBDS
- C3 - Corrosion from by-products of sulfur
- C4 - Corrosion by metals without sulfur