Techniques de décontamination
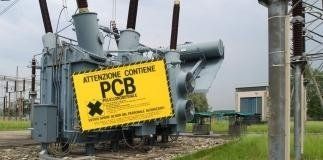
Pour résoudre le problème des PCB contenus dans les huiles de transformateur (ou d'autre matériel électrique), il faut donc descendre en dessous de 50 mg/kg, mieux encore, en dessous de 25 mg/kg afin de pouvoir livrer l'huile gratuitement au Consortium des huiles usagées (COOU).
Pour l'identification et la sélection des techniques de décontamination des PCB, le document de référence sont sans doute les Lignes directrices du Ministère de l'Environnement(décret ministériel du 21/01/2007). Ce document identifie deux types de solutions alternatives :
- Le remplacement du liquide isolant (Remplissage) avec du liquide isolant neuf, et la mise au rebut du liquide isolant utilisé comme un déchet PCB. (TECHNOLOGIE DE COMBUSTION).
- La déshalogénation (décontamination) des PCB dans le liquide isolant en service, qui permet de maintenir l'utilisation de l'huile contaminée après un traitement de désintoxication (d'élimination) des PCB. (TECHNOLOGIE SANS COMBUSTION).
Les principaux procédés chimiques actuellement disponibles sont les suivants :
- Procédés de déshalogénation au sodium, lithium et dérivés,
caractérisés par :
- réactifs liquides dangereux à base de sodium métallique, hydrure de sodium, hydrure de lithium
- un processus discontinu qui rend l'ensemble de l'opération encore plus difficile
- des températures moyennes de fonctionnement élevées (150 à 300 °C), ce qui augmente le risque d'explosion en particulier en présence d'eau et d'air
- Processus de déshalogénation avec du polyéthylène glycol et de l'hydroxyde de potassium (KPEG en batch).
Cette technique :
- utilise un réactif liquide constitué par le polyéthylène glycol (PEG) et un hydroxyde de métal alcalin (en général, KOH), et présente donc une séparation difficile du réactif liquide et des produits de réaction de l'huile isolante
- fonctionne à des températures de 130 à 150 °C
- a une efficacité limitée sur certains types de contaminants (Aroclor 1242)
- Processus de déshalogénation en continu en circuit fermé
Cette technologie :
- emploie un réactif solide breveté, efficace mêle sur les halogénures aromatiques particulièrement stables
- fonctionne à des températures de 80 à 100 °C
- ne produit pas de déchets
- peut être réalisée sur le site d'installation du matériel à décontaminer, au moyen de la circulation fermée de l'huile, sans avoir à vidanger le matériel, même partiellement.
La seule technologie qui fonctionne selon ces caractéristiques est le CDP Process® de Sea Marconi
Les Lignes directrices du Ministère de l'Environnement(décret ministériel du 21/01/2007), en plus d'établir une liste et de décrire en détail les différentes méthodes de décontamination des PCB, identifient les forces et les faiblesses des différentes techniques par rapport aux critères que chaque détenteur devraient envisager, par exemple :
- Aspects environnementaux
La préférence doit être donnée aux techniques de décontamination permettant de récupérer l'huile et la machine, par rapport au remplacement et à l'élimination du liquide isolant (retrofilling). En plus de mettre l'accent sur les techniques qui opèrent sur place sans avoir à vidanger le transformateur grâce au fait qu'elles reflètent les principes de proximité, d'autosuffisance et de récupération fonctionnelle énoncés dans les directives communautaires. Enfin, les procédés mis en œuvre en continu, en cycle fermé, sans vidanger les matériels, sont intrinsèquement plus sûrs par rapport aux risques de déversement de liquides contenant des PCB dans l'environnement.
- Consommation des ressources et écobilan environnemental
- Émissions atmosphériques et bruit
- Production de déchets
Dans ce contexte, les différences entre le changement d'huile et les techniques de déshalogénation technique sont considérables.
Le changement de la charge d'huile implique la génération de déchets dangereux(liquides contenant des PCB et solvants) en une quantité égale ou supérieure à la quantité des PCB contenus dans les matériels, à la suite des phases répétées de vidange et de lavage du matériel.
---
Les techniques de déshalogénation avec des hydrures de métaux alcalins ou de polyéthylène glycol et de l'hydroxyde de potassium (qui NE SONT PAS utilisées par Sea Marconi) génèrent des déchets liquides et solides résultant des étapes de réaction, de filtration et d'absorption dans une quantité inférieure à la quantité du liquide isolant décontaminé (10 à 15 %), généralement en fonction de la concentration de PCB initiale et des seuils à atteindre. Toutefois, les phases de transport et d'élimination des déchets contenant du sodium, du lithium et des dérivés s'avèrent problématiques en raison de leurs caractéristiques de dangerosité intrinsèque.
---
La technique de déshalogénation (utilisée par Sea Marconi) ne génère pas de déchets dangereux. Les réactifs et les autres matériaux utilisés pour le traitement peuvent être utilisés à plusieurs reprises dans des procédés de décontamination similaires jusqu'à la fin de leurs propriétés réactives.
- Analyse des risques pour la sécurité des travailleurs et la santé publique
- Risques d'explosion et d'incendie des matériels
- Risques de fuites et de déversements dans l'environnement
De ce point de vue, il faut évidemment privilégier les techniques de décontamination qui agissent dans un cycle fermé et sans vidanger les matériels, même partiellement.
---
Le changement d'huile (remplissage) est certainement la technique la plus pénalisée en raison de la manipulation et du déversement d'énormes volumes de liquides isolants.
- analyse du contexte opérationnel et des contraintes logistiques
- certification
- expérience opérationnelle de l'opérateur
Les lignes directrices du Ministère de l'Environnement(décret ministériel du 21/01/2007) concluent en indiquant que les meilleures techniques disponibles (MTD) sont les suivantes :
- celles qui emploient la déshalogénation en continu en circuit fermé, c'est-à-dire le CDP Process® de Sea Marconi pour les transformateurs ou les matériels « en service » et « en fin de vie » contaminés par les PCB
- le remplacement d'huile + CDP Process ® pour transformateurs ou matériels « en service » isolés en PCB
- décontamination + procédés de récupération des matières solides constituant la machine pour transformateurs ou pour équipements électriques « en fin de vie » isolés en PCB
Cliquez sur l'image pour l'agrandir.