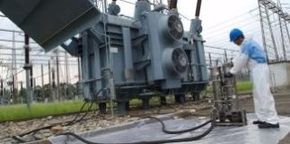
Filling under vacuum and oil treatment
These treatments are applied in the following cases:
- first filling of new machines arriving at the installation site containing dry nitrogen in slight overpressure
- following maintenance work that required partial or total emptying of oil
The requirements of this specification apply to high power
equipment at maximum voltage exceeding 72.5 kV, filled with inhibited or uninhibited
mineral insulating oils, the origins of which meet the specifications of IEC standard 60296
The service includes the following activities:
- Two-way transport of personnel, technological systems and equipment from Sea Marconi to the places of service delivery indicated by the customer
- Site installation and preparation, hydraulic and electrical connection of the treatment systems
- DEOSVISION® analysis of quality control of new oil
- Preliminary treatment of new oil
- Preparation of transformer for vacuum
- Application of vacuum
- Partial filling under vacuum
- Final filling and checking of levels and vents
- Filling of accessories
- Final oil treatment
- DEOSVISION® analysis of quality control at end of intervention
Inhibition
Following depolarisation from corrosive sulfur treatments and consequent elimination of DBDS, it may be necessary to restore the oxidation stability of the oil through addition of an anti-oxidant additive such as DBPC (2,6-ditertiarybutyl para-cresol) or ditertiary-butyl phenol.
Passivation
The problem of corrosive sulfur can be solved effectively and durably only through Chedcos selective depolarisation; nevertheless ( read here ) Sea Marconi can also carry out passivation treatment which tends, however, to lose its effectiveness over time.
This operation involves adding a passivator additive (ToluilTriazolAmine or Ciba-Irgamet 39 or NyPass) to the corrosive oil in order to protect copper surfaces against the attack of corrosive compounds such as DBDS.