Corrosiveness of oils
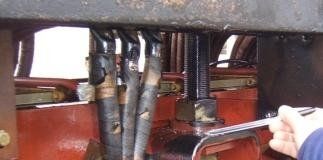
The term corrosive sulfur generically refers to the corrosive properties of some types of oils that have caused, and continue to cause, numerous failures in electrical equipment (transformers, reactors, etc.) in networks around the world.
The main cause of this corrosivity
was actually identified by Sea Marconi's R&D in 2005; through an innovative analytical technique, our laboratory surprisingly identified the DBDS(dibenzyl disulfide) molecule in naphthenic oils produced between 1993 and 2009.
This additive, added to the oil during the refining process to improve oxidation stability, tends to combine with the copper present in the transformer forming copper sulfide; this compound is deposited on the copper surfaces of the windings, in a manner similar to rust.
The copper sulfide then tends to detach from the copper and circulate dangerously in the oil, gradually being deposited within the highly porous insulating pressboards.
The natural consequence of this phenomenon is weakening of the insulation
up to the electric arc and failure, with consequent direct damage(loss of the machine) and indirect damage(loss of production). The process is manifested in different ways depending on the type of oil and at different times depending on the temperature and the modes of operation of the transformer.
In recent months, our R&D has also shown how there are enormous problems related to corrosiveness in non-naphthenic oils and, in any case, in products even before 1993, which is why Sea Marconi classifies corrosive oils into 4 different typologies:
- C1 - Corrosion with DBDS
- C2 - Corrosion without DBDS
- C3 - Corrosion from by-products of sulfur deterioration
- C4 - Corrosion by non-sulfurised metals
Click on image to enlarge