How to establish corrosiveness
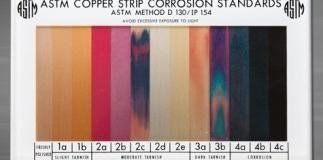
The issue of corrosivity is certainly very complex and only through a gradual approach can the mechanisms, diagnostic indicators, countermeasures, etc. be understood.
For the establishment of corrosive sulfur, the reference standard (and that from which to start) is IEC standard 60422 ed. 4, 2013, and that is the norm for the maintenance and supervision of mineral insulating oils in electrical equipment in service. This standard indicates three methods for the test of corrosive sulfur:
1. IEC 62535
– commonly called the CCD Test.
Test technique:
Accelerated oxidation at high temperature of the copper conductor wrapped in kraft paper, visual assessment (ex method Cigre A2.32.TF01)
Purpose: Establish the presence of sulfur compounds with corrosive action that could contaminate the cellulose of conductors with copper sulfide.
2. ASTM D1275, Method B
Test technique:
Accelerated oxidation at high temperature of the electrolytic copper strip, visual assessment for 48 hours at 150 °C (Method A: 19 hours at 140 °C)
Purpose: Establish the presence of sulfur compounds with corrosive action that could contaminate copper surfaces.
3. DIN 51353
Test technique:
Accelerated oxidation at high temperature of the silver strip, visual assessment.
Purpose: Establish the presence of sulfur compounds with corrosive action that could contaminate silver surfaces.
To these tests should certainly be associated the DBDS test (IEC 62697-1: 2012, Test methods for quantitative determination of corrosive sulfur compounds in unused and used insulating liquids - Part 1: Test method for quantitative determination of dibenzyl disulfide (DBDS)), the main corrosive substance in mineral insulating oil, and the IFED test, a sort of fingerprint of the oil which, in the diagnostic phase, enables understanding if the oil is one of those known as corrosive.
International sector standards are excellent and indispensable guidelines but there are cases where the slow approval process (not less than three years) makes them unable to provide adequate countermeasures for critical problems with equipment. The issue of corrosiveness is a case in point: it is in continuous evolution and standards are lagging behind the answers that owners need.
Neglecting the DIN 51353 test, which is useful for checking the oil corrosion on transformer accessories with silver contacts, neither the CCD nor the ASTM D1275 tests are able to exclude all cases of corrosiveness, because they are empirical and qualitative methods.
Interpretative doubts may arise (see IEC 62535): false negative
in the presence of additives or false positives
in the case of oils that are particularly oxidised (see IEC 62697). Furthermore, there are also cases where oil corrosion is caused by sulfur compounds
that are difficult to establish.
TCS (Total Corrosive Sulfur) in accordance with IEC 62697 Part 2 - Test methods for quantitative determination of Total Corrosive Sulfur (TCS).
In-depth analysis and diagnosis are therefore necessary that exclude the cases mentioned above. To this end, Sea Marconi has developed a test included in IEC 62697 called TCS(Total Corrosive Sulfur), which is able to offer a quantitative answer on the corrosive sulfur compounds
present in the oil, independently of oxidation of the oil and the presence of the additives.
The test can also be performed by the customer using the special SM-TCS kit.
The tests hitherto described are able to detect or exclude the vast majority of cases of corrosiveness, but there are recent studies which are shedding light on new mechanisms of corrosion. These case studies, rarer but nevertheless already documented, require specific analytical investigations and a detailed diagnosis in each case.
Click on image to enlarge