Countermeasures for the problem
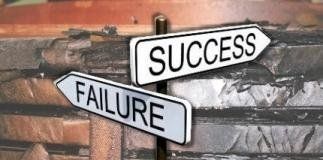
There are basically two approaches on the market for trying to solve the phenomenon of corrosion caused by DBDS: oil replacement or passivation, which is the addition of a substance (passivator) to the oil that should protect the copper parts inside the transformer. However, it should be noted that neither oil replacement nor passivation can be considered solutions to the problem for the following reasons:
Oil replacement
In addition to being expensive, oil replacement is not able to completely eliminate DBDS and, above all, it is not able to block the effects of the copper sulfide already deposited in the inner parts of the pressboards.
Passivation
It is particularly important to clarify that
passivation does not eliminate DBDS .
In theory, passivation should form a layer on copper surfaces in order to prevent attack by corrosive sulfur compounds (such as DBDS), but it has been scientifically demonstrated that the protective film is
extremely weak and already tends to lose effectiveness in the short term. The most important factor to consider is that
the passivator has no effect against the action of the copper sulfide as has already been demonstrated in cases of documented failures:
CIGRE No. 378/2-2009
"
4.1.1 Experiences (C) .. However, the addition of metal
passivators is not a guarantee against failures. For instance, in Brazil, more than 200 shunt reactor oils in service were passivated (in most cases between ½ and 2 years after going into service). It has been reported that 9 of these units failed between one and 24 months after passivation
. One explanation for these failures,which led to very corrosive oils and high thermal loads, is that deposition took place very quickly (in the first months after start-up),
following which passivation was ineffective
.(C). ”
So what is to be done?
Currently, the Chedcos ® selective depolarisation process is the only truly effective, and above all lasting, solution to the problem of corrosive sulfur.
CIGRE No. 378/2-2009
4.2
Removal of corrosive sulfur from oil in service
(C). Several techniques have been proposed, and in some cases are already being used for the removal of corrosive sulfur from oil. These include the use of :
-
continuous on-line treatment with sorbents
;
-
“selective depolarisation” (a combination of reagents and sorbents)
;
PASSIVATION | OIL CHANGE | DEPOLARIZATION | |
---|---|---|---|
Simplicity | High | Low/Medium | Low/medium |
Duration | Low | Low/Medium | Medium/high |
Under load | No | No | S |
Efficiency | Low | Medium/high | High |
Improvement of the oil's properties | No | S | S |
Performance durability | Low | High | High |
Environment | Unknown | Low | High |
Cost/Benefit | Very low | Medium/High | High |